In the fast-paced world of manufacturing, efficiency and cost-effectiveness are paramount. As industries strive to optimize their operations, predictive maintenance has emerged as a game-changer. This proactive approach not only minimizes downtime but also significantly reduces maintenance costs, ultimately leading to enhanced productivity. This article delves into the concept of predictive maintenance, its benefits, challenges, and the future it holds for the manufacturing sector.
Understanding Predictive Maintenance
Predictive maintenance refers to the use of advanced technologies and data analysis to predict when equipment will fail or require servicing. By monitoring the condition of machinery in real-time, manufacturers can schedule maintenance activities at the most opportune moments, thereby avoiding unexpected breakdowns. This proactive approach not only enhances operational efficiency but also significantly reduces costs associated with unplanned downtime and emergency repairs, making it a vital strategy in today’s competitive manufacturing landscape.
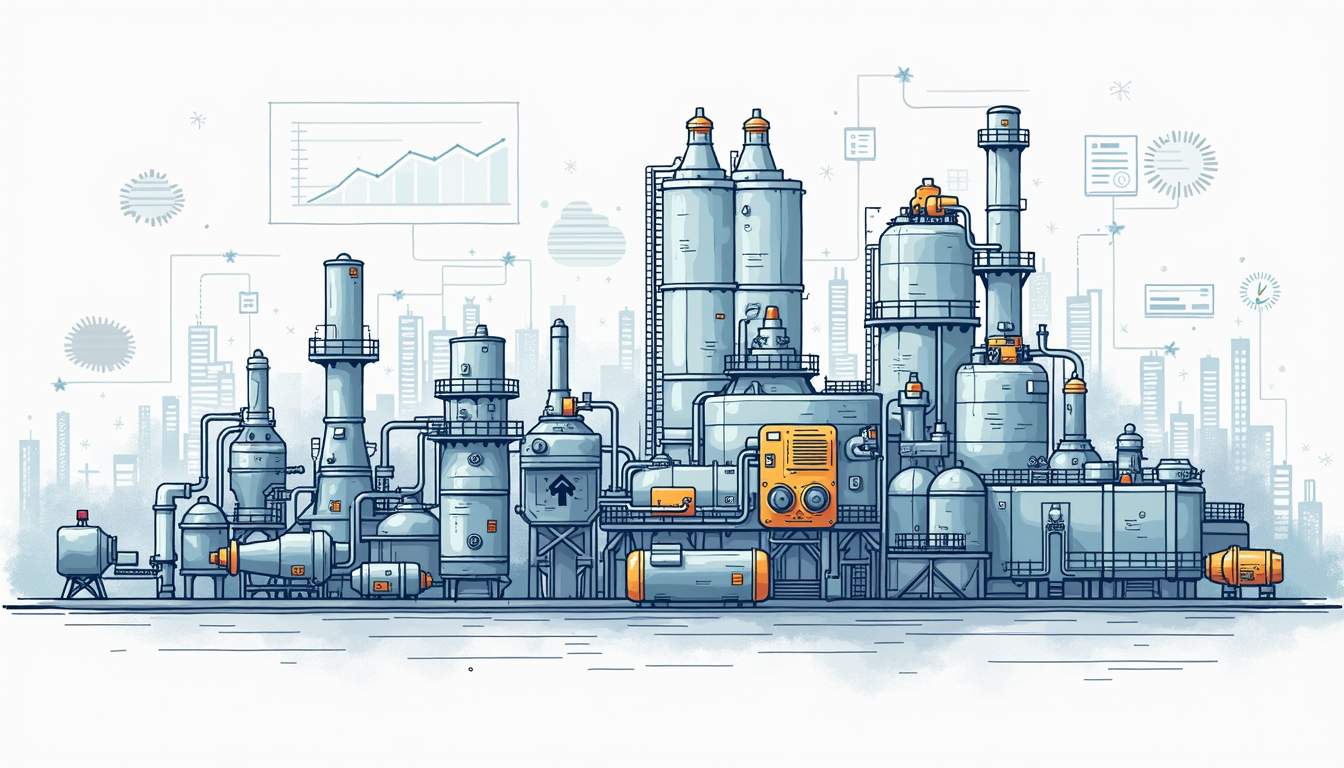
The Technology Behind Predictive Maintenance
At the heart of predictive maintenance lies a combination of IoT (Internet of Things) sensors, machine learning algorithms, and data analytics. These technologies work together to collect and analyze data from machinery, providing valuable insights into their operational health. The integration of these technologies allows for a seamless flow of information, enabling manufacturers to make informed decisions based on real-time data rather than relying solely on historical maintenance records.
IoT sensors are installed on various equipment, continuously gathering data on parameters such as temperature, vibration, and pressure. This information is then transmitted to a centralized system, where machine learning algorithms analyze it to identify patterns and predict potential failures. The result is a robust maintenance strategy that allows manufacturers to stay ahead of equipment issues. Moreover, as these systems learn from ongoing data collection, their predictive capabilities improve over time, leading to increasingly accurate forecasts of machinery performance and maintenance needs.
Key Components of Predictive Maintenance
Several key components contribute to the success of predictive maintenance in the manufacturing industry:
- Data Collection: Continuous monitoring of machinery through sensors ensures that accurate data is always available.
- Data Analysis: Advanced algorithms analyze the collected data to identify trends and predict failures.
- Actionable Insights: The analysis provides actionable insights that guide maintenance scheduling and decision-making.
In addition to these components, the implementation of a user-friendly dashboard is crucial for effective communication of insights to maintenance teams. This dashboard can visualize data trends and alerts, making it easier for technicians to prioritize tasks based on urgency and impact. Furthermore, integrating predictive maintenance with other systems, such as inventory management and supply chain logistics, can optimize resource allocation and ensure that necessary parts are available when maintenance is scheduled. Such comprehensive integration fosters a more resilient manufacturing environment, capable of adapting to both routine and unexpected challenges.
Benefits of Predictive Maintenance
The adoption of predictive maintenance offers numerous advantages that can significantly enhance operational efficiency and reduce costs.
Minimized Downtime
One of the most significant benefits of predictive maintenance is the reduction of unplanned downtime. Traditional maintenance strategies often rely on reactive approaches, where equipment is serviced only after a failure occurs. This can lead to extended downtime and lost production time.
In contrast, predictive maintenance allows manufacturers to anticipate equipment failures and perform maintenance before issues arise. This proactive approach ensures that machinery operates smoothly, minimizing disruptions in production schedules. By utilizing advanced data analytics and real-time monitoring, companies can gain insights into equipment health, enabling them to schedule maintenance during planned downtimes rather than interrupting critical operations.
Moreover, the integration of IoT (Internet of Things) devices into machinery enhances the predictive capabilities, as these devices continuously collect and transmit data regarding performance metrics. This not only aids in identifying potential failures but also helps in fine-tuning operational processes, leading to a more streamlined workflow and improved overall productivity.
Cost Savings
Predictive maintenance can lead to substantial cost savings for manufacturers. By addressing maintenance needs before they escalate into major issues, companies can avoid expensive repairs and replacements. Additionally, optimizing maintenance schedules helps in reducing labor costs and extending the lifespan of equipment.
Furthermore, the ability to predict failures allows manufacturers to maintain optimal inventory levels for spare parts, reducing excess stock and associated carrying costs. This strategic inventory management not only saves money but also ensures that critical components are available when needed, thus preventing delays in production.
In addition to direct cost savings, predictive maintenance can enhance the overall return on investment (ROI) for manufacturing operations. By improving equipment reliability and performance, companies can increase their output and efficiency, leading to higher revenue generation. The long-term benefits of adopting predictive maintenance extend beyond immediate financial gains, fostering a culture of continuous improvement and innovation within the organization, ultimately positioning them as leaders in their respective industries.
Challenges in Implementing Predictive Maintenance
While the benefits of predictive maintenance are clear, implementing such a strategy is not without its challenges. Manufacturers must navigate several obstacles to successfully adopt predictive maintenance practices.
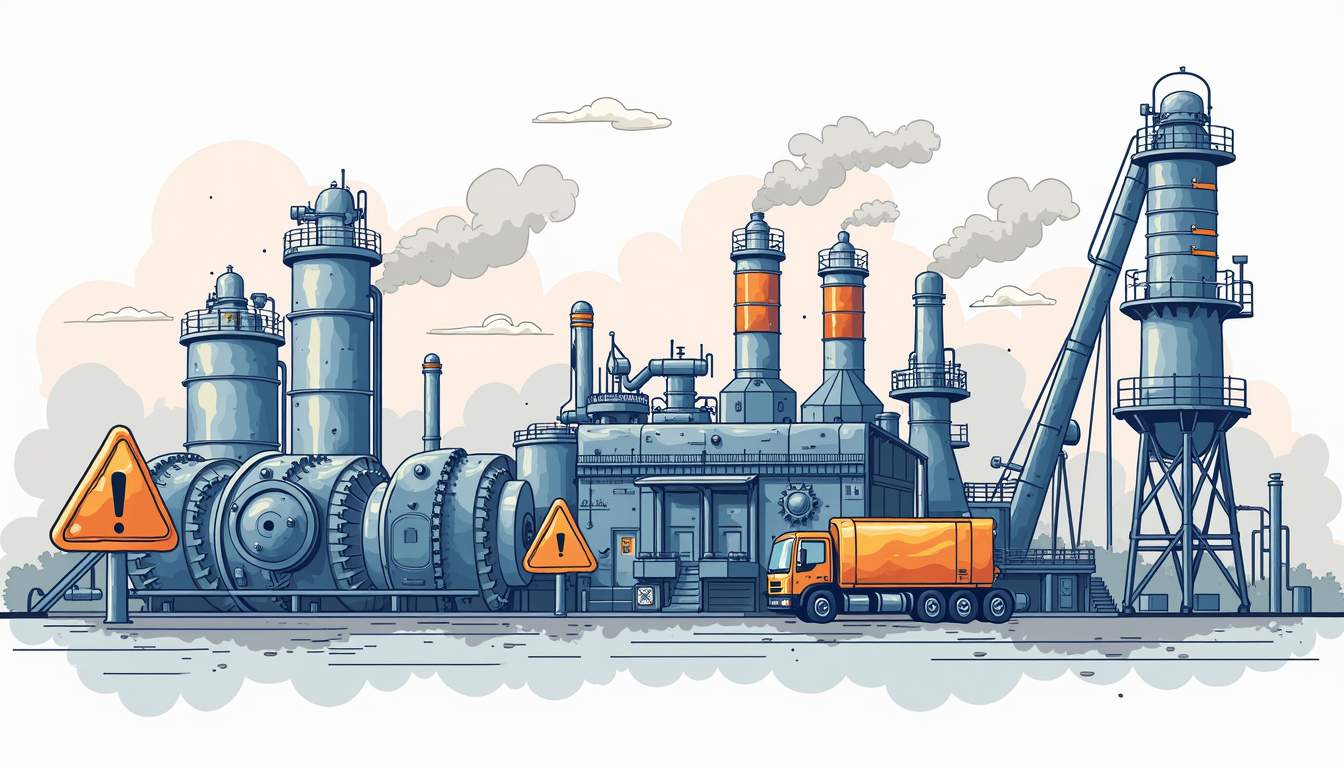
Data Management and Integration
One of the primary challenges in predictive maintenance is managing and integrating the vast amounts of data generated by IoT sensors. Manufacturers must invest in robust data storage and processing systems to ensure that data is not only collected but also analyzed effectively.
Moreover, integrating predictive maintenance systems with existing manufacturing processes and equipment can be complex. Companies must ensure that their workforce is trained to utilize these new technologies and that there is a seamless flow of information between different systems. This often requires a cultural shift within the organization, where employees must embrace data-driven decision-making and adapt to new workflows that incorporate predictive analytics.
Additionally, the quality of the data collected is paramount. Inaccurate or incomplete data can lead to erroneous predictions, ultimately undermining the entire predictive maintenance strategy. Therefore, manufacturers must establish strict data governance protocols to ensure that the information being analyzed is both reliable and actionable.
Cost of Implementation
While predictive maintenance can lead to long-term cost savings, the initial investment can be significant. Companies must consider the costs associated with purchasing IoT sensors, software solutions, and training personnel. For smaller manufacturers, this upfront investment may pose a barrier to entry.
Furthermore, the ongoing costs associated with maintaining and updating these systems can also add up over time. As technology evolves, manufacturers need to stay ahead of the curve by regularly upgrading their tools and software to leverage the latest advancements in predictive analytics. This can create a continuous cycle of investment that some companies may find difficult to sustain, particularly if they are not yet reaping the anticipated benefits of their predictive maintenance initiatives.
Moreover, the return on investment (ROI) for predictive maintenance can be difficult to quantify in the early stages. Companies may struggle to measure the direct impact of their predictive maintenance efforts, making it challenging to justify the costs involved to stakeholders. This uncertainty can lead to hesitation in fully committing to predictive maintenance strategies, as decision-makers weigh the potential risks against the promise of future savings and efficiency gains.
Real-World Applications of Predictive Maintenance
Numerous manufacturers across various industries have successfully implemented predictive maintenance strategies, leading to remarkable improvements in efficiency and cost savings.
Automotive Industry
The automotive industry has been at the forefront of adopting predictive maintenance. Major manufacturers utilize advanced analytics to monitor the health of assembly line machinery. By predicting potential failures, they can schedule maintenance during non-peak hours, ensuring that production remains uninterrupted.
For instance, a leading automotive manufacturer implemented a predictive maintenance program that reduced equipment downtime by 30%. This not only improved production efficiency but also resulted in significant cost savings over time.
Aerospace Sector
The aerospace sector also benefits greatly from predictive maintenance. Airlines and manufacturers of aircraft components employ data analytics to monitor engines and other critical systems. By predicting when maintenance is required, they enhance safety and reliability while minimizing operational disruptions.
One notable example is an airline that adopted predictive maintenance for its fleet, resulting in a 25% reduction in maintenance costs and improved on-time performance. This success underscores the potential of predictive maintenance in high-stakes industries.
The Future of Predictive Maintenance
As technology continues to evolve, the future of predictive maintenance in the manufacturing industry looks promising. Several trends are expected to shape its development in the coming years.
Artificial Intelligence and Machine Learning
The integration of artificial intelligence (AI) and advanced machine learning algorithms will further enhance predictive maintenance capabilities. These technologies will enable more accurate predictions by analyzing larger datasets and identifying complex patterns that may not be apparent through traditional methods.
As AI continues to improve, manufacturers can expect even greater reductions in downtime and maintenance costs, leading to a more efficient production environment.
Cloud Computing and Big Data
The rise of cloud computing and big data analytics will also play a crucial role in the future of predictive maintenance. By leveraging cloud-based platforms, manufacturers can access and analyze data from multiple sources, allowing for a more comprehensive view of equipment health.
This interconnected approach will enable manufacturers to make data-driven decisions quickly and efficiently, ultimately enhancing their predictive maintenance strategies.
Conclusion
Predictive maintenance is revolutionizing the manufacturing industry by enhancing efficiency and driving cost savings. By leveraging advanced technologies and data analytics, manufacturers can anticipate equipment failures, minimize downtime, and optimize maintenance schedules.
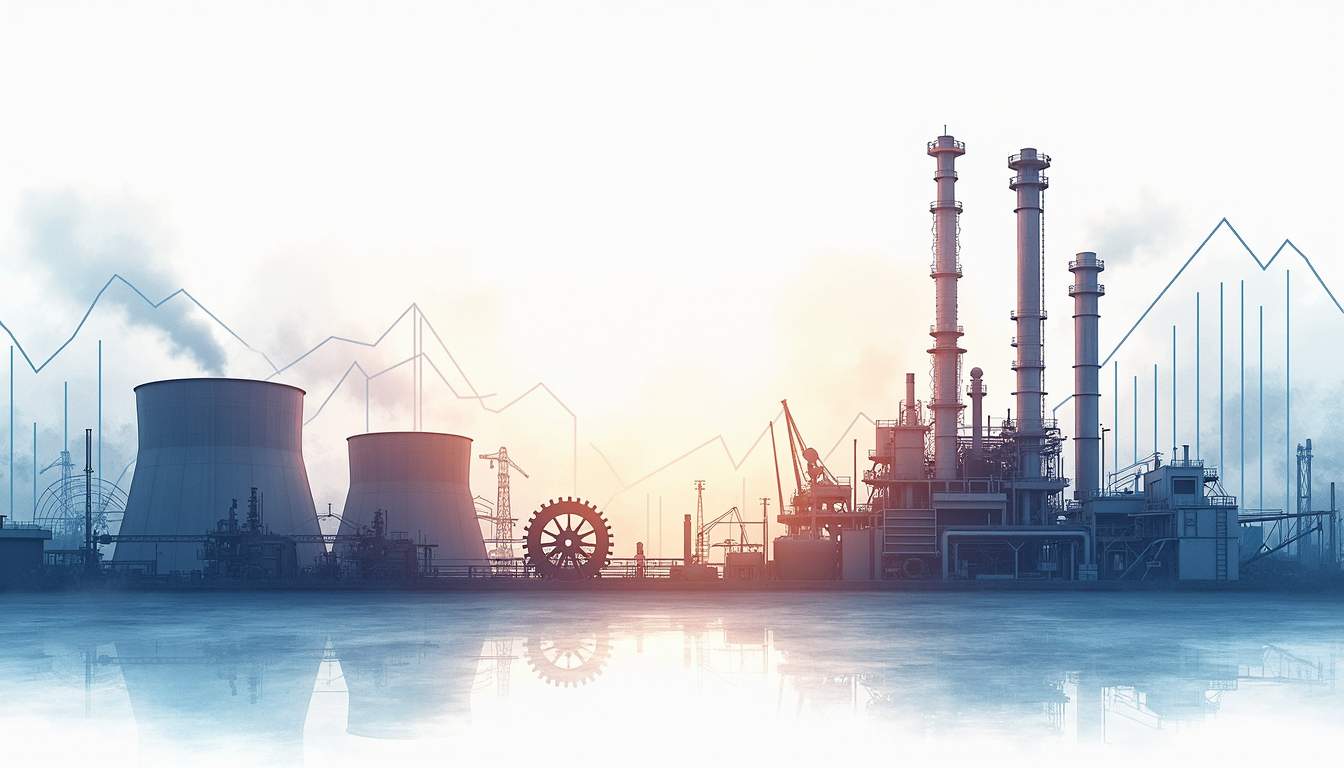
While challenges remain in implementing predictive maintenance strategies, the benefits far outweigh the obstacles. As technology continues to advance, the future of predictive maintenance looks bright, promising even greater efficiencies and innovations in the manufacturing sector.
In conclusion, embracing predictive maintenance is not just a trend; it is a critical step for manufacturers aiming to thrive in an increasingly competitive landscape. By investing in predictive maintenance, companies can ensure they remain at the forefront of the industry, ready to tackle the challenges of tomorrow.
Take the Next Step with Cybersort
Ready to unlock the full potential of predictive maintenance in your manufacturing operations? Cybersort is here to enhance your digital infrastructure, ensuring maximum efficiency and security. Gain the visibility and control you need for safer operations and a successful digital transformation. Don’t miss the opportunity to lead your industry into the future. Book a discovery call with us today and take the first step towards revolutionizing your plant’s maintenance strategy.